Continuous Stress Monitoring of Large Structures
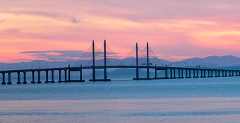
Continuous stress monitoring of large structures using an updated finite element model and displacements measured at a limited number of GPS receiver locations.
Written by: Eddy Dascotte, Jacques Strobbe, Ulf T. Tygesen
The original article can be found in: www.femtools.com
INTRODUCTION
A common goal of vibration monitoring systems is to perform Accumulated Fatigue Monitoring (AFM). Ideally, to support AFM, is it required to determine the stress histories anywhere in the monitored structure under real measured loading conditions.
Computational determination of stress histories is usually suffering from large uncertainties. Experimentally, stress histories are determined from strain gauges, but high-stress regions and joints may be difficult, or even impossible, to instrument, for example if below water on offshore structures. Furthermore strain gauges are fragile and therefore not reliable for long time measurements.
Stress histories at any location can be efficiently obtained by combining a finite element model and measurements of displacement and strain histories at only a number of selected locations. Using the computed mode shapes of the structure, the corresponding modal forces and moments in all the elements of the structure and the experimental time histories, a modal expansion procedure is applied to obtain the forces and moments time histories in any element of the structure.
The success of this combined numerical-experimental approach depends on the validity of the finite element model and of the modal expansion procedure that will estimate the local stresses in the structure from recombined modal stresses. A brief overview of the system components is presented hereafter and demonstrated using two real-life large structures: a stay-cable bridge (Stonecutters Bridge in Hong Kong), and an offshore oil platform (Valdemar platform in the Danish North Sea).
A SYSTEM FOR CONTINUOUS STRESS MONITORING
The stress monitoring system consists of tools for pre-test analysis, operational modal analysis, finite element model updating, modal expansion and stress recovery.
Pre-test Analysis
A pre-test analysis and verification phase consists of simulating the fatigue monitoring process for demonstration purposes, and to check the feasibility under assumed measurement conditions. The simulation uses an existing finite element model with realistic dynamic loading. Strain and displacement time histories at a number of selected locations are simulated and will be used subsequently as ‘experimental data’. The selected locations correspond with the assumed location of commonly available measurement sensors like strain gauges and GPS receivers respectively. Verification of the selected configuration can be done by comparing the forces and moments time histories obtained by the expansion procedure with the results obtained by simulation.
Operational Modal Analysis
Dynamic features monitoring refers to the use of accelerometers to extract the global modal parameters of large structures such as modal resonant frequencies, mode shapes, and modal damping by means of Operational Modal Analysis (OMA). These modal parameters form the bases for subsequent dynamic analyses of operational load effects, like wind, waves, traffic and seismic loads, for updating and refinement of the finite element models, and for supplying data to the structural health monitoring and evaluation systems. A high level of automation is required for continuous operational modal analysis with only minimal human intervention.
Finite Element Model Updating
Finite element model updating is a necessary step to validate a finite element model and to adjust estimates for uncertain input parameters. To update a finite element model, the analyst needs access to the parameters defining the model, and the responses that are compared against experimentally obtained reference values. Once defined, the updating software will compute sensitivity (‘rate of change of the responses for changes of the parameters’) and estimate the required parameter changes to reduce the overall differences between the reference response values and the actual analytical responses.
For large structures, the reference data are in general modal parameters (frequencies, mode shapes) obtained by operational modal analysis. The selection of updating parameters is key to succesfully increasing confidence in the FE model. Updating parameters may include material properties, equivalent geometrical properties (thickness, beam cross section, etc), joint stiffness and constraints. Their availability as local or global parameters depends on the finite element program that is used and the interface and driver programs. Very flexible parameter selection is possible if the finite element model and the associated element properties can be completely parsed and made available to the model updating software. Depending on the availability of element mass and stiffness matrices, additional features and performance enhancements are available.
In the general case, however, an interface program and driver can be custom developed, for example to support an in-house proprietary finite element program. In this case, generic parameters can be defined by referencing numbers in the input data file of the finite element program.
Modal-based Expansion and Stress Recovery
Using an updated finite element model, a sparse set of displacements measured at GPS receiver locations can be expanded using a modal-based method to obtain displacements at all FE node locations. The transformation matrix that is used by this expansion process can also be applied to obtain forces, moments, strain, or stress at any location in the bridge. This is a very efficient process that can be performed on real-time or historical GPS data and requires only minimal data storage capacity and computational effort.
The validity of the process depends on the refinement of the finite element model, the proper choice of sensor locations and a sufficient number of mode shapes. The finite element model will have to be continuously updated to account for any structural changes in the structure during its lifetime. Different transformation matrices can be used depending on the displacement amplitudes as a way to consider nonlinear behavior of the bridge.
For very large structures, the use of GPS receivers has been demonstrated to be a practical and accurate type of sensors to construct equation 2 but also data from strain gauges can be included. Using different types of monitoring data requires the introduction of normalized variables.
The required number of mode shapes is to be determined by pre-test analysis but is a priori limited to the modes that can be validated by operational modal analysis. More modes or additional vectors like static deformed shapes can be added if deemed necessary to improve the quality of the expansion procedure.
Hong Kong Stonecutters Bridge
Stonecutters Bridge in Hong Kong is a high-level cable-stayed bridge, with two towers located in the back-up areas of the busy Kwai Chung Container Port which is frequented by the world’s largest container ships. It has a steel main span of 1018 meters across the Rambler Channel and a total length, including the backspans, of some 1.6 km. The vertical clearance is 73.5 meters over the navigation channel. The deck is supported by two 290 meters tall concrete and stainless steel towers. It is 53 meters wide and split into two streamlined boxes connected by ross girders. Stonecutters is the second longest cable-stayed span in the world, and one of only two cable-stayed bridges with a span in excess of 1 km.
A wind and structural health monitoring system (WASHMS) is deployed by Hong Kong Highways Department to monitor the structural performance of Stonecutters Bridge under its designated performance criteria at serviceability limit state and to evaluate possible defects and structural safety when these are exceeded [1-3]. For this purpose a wide array of 1,700+ sensors are deployed, including structural and environmental sensors to measure displacements, strain, acceleration, temperature and wind conditions (Fig. 1). This makes Stonecutters Bridge probably the most heavily instrumented bridge in the world.
Safety requirements have increased the focus on vibration monitoring using acceleration signals and displacements using GPS receivers [4]. The acceleration signals are primarily used for operational modal analysis (OMA) to obtain reference values for validation and updating the finite element models of the bridge [5]. The measured displacements and updated finite element models are used in a hybrid method to compute the strains, stresses, forces and moments at any location of the bridge. Vibration monitoring, combined with a structural health evaluation system and fatigue assessment, enhances safety by allowing better planning of inspections and maintenance work.

A customized data processing and analysis system is in operation since 2011 that was developed by DDS using the FEMtools Framework (www.femtools.com). The system consists of the following components: (a) Operational modal analysis from acceleration time histories. Modal extraction is automated and is used for model updating, and monitoring of modal parameters. (b) Displacement monitoring using GPS receivers. The displacement data serves as input for stress recovery at any location using a finite element model of the bridge. The stresses are used for accumulated fatigue monitoring. (c) Correlation of stress, force and moments with environmental conditions (wind, temperature).
Operational Modal Analysis
Modal parameters extraction is done using two industry-standard OMA methods: i) Stochastic Subspace Identification (SSI) using external stand-alone software and (ii) Polyreference Least Squares Complex Frequency-Domain Estimator (pLSCF) that is integrated in the Stonecutters Bridge WASHMS monitoring software. Comparison revealed high similarity between results obtained with these two different OMA methods, which inspires trust in the obtained mode shapes. Both methods produce very clear stabilization diagrams and are therefore suitable for automation of the pole selection process. The built-in OMA using pLSCF is more suitable for automatic processing as it enables a smooth data flow between the acceleration data reader and the tools that make use of mode shapes.
The influence of the recording length was studied and showed that with three hours recording the same number of mode shapes can be obtained as with one hour recording on a day with strong winds. Averaging of the signals that are acquired at both sides of the bridge deck also improves the possibility to extract more mode shapes. Monitoring over longer periods of time learned that resonant frequencies remain very stable throughout the day while modal damping increases and varies significantly during heavy traffic hours.
Stress Recovery and Fatigue Assessment
Using custom-developed data processing routines, displacements of 8 GPS receivers are retrieved from an SQL database for further processing by a program for displacement and stress monitoring (Fig 2). The GPS system converts the raw GPS signals (longitude, latitude and height) to displacements of the GPS receivers in the bridge coordinate system prior to storage in the SQL database.
They are located at the tower tops, and at both sides of the bridge deck at 1/4, 1/2 and 3/4 span. The displacements obtained by the GPS system (Leica) are said to be accurate to +/- 2 cm. This is achieved by using an error correction signal emitted by a reference transmitter on the ground with an exactly known position. The sampling rate is 20 Hz. The atmospheric conditions in Hong Kong are in general suitable for the proper functioning of the GPS system. However, during passing of heavy clouds the performance of the system may be negatively influenced. During the test period it was observed that GPS signals sometimes show spurious behavior or become temporarily unavailable. Appropriate signal processing is therefore mandatory to condition the data (i.e. removal of outliers, interpolation of missed measurements,…).
Knowing the stresses resulting from the actual deformation of the bridge during its service life is desirable as they provide input to an accumulated fatigue monitoring procedure. This will allow to assess the remaining residual life time from the 120-years design life time. In practice, the information on the actual loading that the bridge was subjected to is mainly used to support decision-making about the inspection and maintenance intervals.
Although stresses will also be computed using various updated finite element models of the bridge, and using statistical and probabilistic load information obtained by the WASHMS sensors (more specifically wind, temperature, traffic and seismic), the GPS system with stress recovery provides an alternative by recording and monitoring the actual deformation of the bridge at all times. This is especially true for incidental loading situations like vessel collisions or extreme transient loading like during typhoons or earthquakes.
The strain and stress data obtained by the recovery process can be used as an alternative to strain recording using strain gauges. During the initial service life, the recorded strain data will remain the primary source for fatigue monitoring using rainflow counting and Miner’s rule. They also serve as references for finite element model validation and updating. The economies that can be realized with the GPS-based approach are, however, significant and therefore it is expected that with time, as confidence in the process builds up, the need for continuous strain recording may be re-evaluated.

Correlation with Wind and Temperature Data
Large cable-stayed bridges like Stonecutters Bridge are subject to varying environmental conditions such as temperature and wind. These environmental effects cause changes in displacements and modal properties, which may mask the changes caused by structural damage. Additional data readers have been developed to retrieve recorded environmental data from the central database. This includes wind speed, direction, power spectrum and temperatures at different locations on the bridge. They are used for correlation against modal parameters, maximal displacements of the deck and towers, and tower base forces and moments.
Postprocessing of the results includes producing scatter plots and histograms, computing various statistical quantities or performing regression analysis. This information helps bridge engineers to gain understanding of the variability of monitoring parameters which is needed by the subsequent structural health rating and evaluation systems.
A novel system for continuous stress monitoring of large structures was presented. The system uses measurements of displacements (GPS) and strain histories in just a few locations as well as a validated and updated finite element model. A modal-based expansion method is used to obtain stress histories in all elements and joints of the structure.
The process has been implemented on a stay-cable bridge and an offshore oil platform. These examples show the potential for use at different levels of a structural monitoring project from pre-test planning the sensor locations and assessing the accuracies of the measurements, over FE model updating to accumulated fatigue monitoring and residual lifetime estimation.
The work done so far constitutes the basis for further development such as initiatives for improvement of data quality from GPS stations with large baselines, nonlinear system identification, FE model updating to non-linear phenomena, and improvement of loading formulations.