Offshore Structural Dynamic Monitoring
Regardless of design life, lifetime of offshore oil and gas structures can vary greatly, when exposed to extreme weather conditions, failure in corrosion control, unexpected dynamic forces, and accumulated fatigue damage. Owing to economic sense, or remaining oil/gas reserves, operators are motivated to extend the life of ageing structures with various methods of life extension measures.
Structural Health Monitoring System (SHMS) is non-invasive, cost effective method backed by sound engineering principles and proven way of damage detection and life expectancy prediction. SHMS can be coupled with real time information and early warning systems for adequate in-time notification of structural failures.
Monitoring system alone will measure the physical condition of the structure, probably with historical data, if monitoring program is already implemented for some time. Coupling with the OMA analysis and FE model updating, monitoring parameters add real-time information, with the ultimate goal of creating and maintaining the continuously updated intelligent digital twin of the structure.
Other inspection protocols, such as corrosion, marine growth, cracks and structural deformations can be easily inserted in the digital twin model for modelling of accumulated damage, degradation and remaining useful life.
Invicom integrates and provides Offshore Structural Dynamic Monitoring systems which are well suited for short or long term monitoring for variety of offshore platforms. Reliable information on the condition of structure is obtained with the carefully engineered integration of:
- Structural sensors (accelerometers, strain gages, displacement probes, tilt sensors)
- Environmental sensors (Wave height radar, water current sensor, wind speed and direction sensors)
- Non-traditional sensors for structural movement (GPS base station)
- Measurement system with self start, automatic power failure logic, internal storage
- Make full use of internet capable devices, iiot, edge computing and cloud based solution
- Analysis software for Damage Detection, FEA with accurately updated model incorporating existing conditions with the goal of providing structural custodians with reliable, accurate and intelligent digital twin, with multiple physical parameters.
Accelerometers
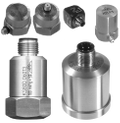
Accelerometers are carefully selected to measure the structural movement down to very low frequencies. General purpose accelerometers cannot be used for large structural monitoring since the frequency range does not cover the low frequency requirements of structural monitoring. Servo force balanced accelerometers can be used, but electrical interference can be a problem if long cables are required. Low frequency IEPE accelerometers are used when long cables are necessary to cover the entire platform. Modern structural monitoring systems use more accelerometers than the strain gages due to ease of deployment. For underwater application, pressure hulls are used to get better signal quality and sensor protection.
Our structural monitoring solution includes many accelerometers arranged either single, bi-axial or tri-axial measurement points. More points yield better modal resolution, and better representation of structural mode shapes. In general, the more measurement points used, the better results will be obtained. Careful analysis needs to be done to optimise the number of sensors deployed, in consideration with installation constraints, cabling and data management.
Strain gages
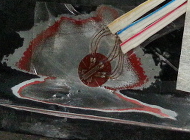
Foil strain gages (gauges) or weldable gages with correct thermally compensated material can be used for measurement of stress levels in structural members to obtain actual dynamic stress levels of the platform. Strain gage application needs careful surface preparation and correct application of bonding cement, wiring and water proofing. Cost of installation for strain gages may be very high for offshore installation.
Displacement probes
Structural deformation can be directly obtained by use of displacement sensors. Global movement cannot be measured using the displacement sensors, since relative movement is required to establish the displacement between reference and moving point. Displacement probes typically measure only single direction of deformation, although there exists sensors with two/three dimensional probes.
Wave height radar and water current sensor
Platform local and global movements are greatly influenced by the height and direction of waves. Continuous changes in tidal conditions influence the damping of structural movements and modal parameters. Wave height measurements simplify the sorting of structural movement with the same wave height and tidal conditions for proper evaluation of modal parameters.
Wind speed and direction sensor
As with wave and tidal conditions, wind speed and direction also play important role on the structural excitation. Wind speed and direction sensors must be positioned in such a way to minimise the influence of the platform itself, to ensure correct wind patterns are recorded and identified.
GPS base station
GPS base station gives absolute platform movement with high accuracy. The station must be installed on the strong structural member to obtain the platform global movement. Due to prohibitively expensive nature of accurate dgps differential measurement systems, it may not be practical for permanent deployment especially when two or more stations are required to obtain torsional as well as translational movements.
Measurement System

With the imc CRONOSflex, we offer a modular system, which gives you an unprecedented degree of flexibility in the setup of your measurement system. The system requires no rack or frame. Both base unit and the measurement modules (amplifiers or conditioners) have independent housings: by a robust “Click Mechanism”, they can easily be either connected directly to one another or alternatively spatially distributed over a standard network cable. A distance of up to 100m between individual modules is possible.
Maximum of 128 channels can be measured with 24 bit resolution and synchronised parallel sampling. If more channels are required, two or more imc CRONOSflex systems can be connected over LAN network and synchronised via built-in synchronisation terminal.
The measurement system accepts multiple input signal types to measure all the sensors with extremely good synchronisation and accuracy. Dissimilar signal types like bridge (Strain gages or Force sensors), voltage, Current, ICP/IEPE and FieldBus (Canbus, Profibus etc) signals can be measured together.
Not only that, excellent low frequency accuracy is provided for big structure monitoring. Since majority of sensors are low frequency IEPE accelerometers, the measurement system’s IEPE signal conditioner is built with special low frequency high pass filter, to match sensor frequency range. imc CRONOSflex ICP/IEPE conditioners can be ordered with high pass frequency as low as 0.07 Hz.
imc CRONOSflex also includes built-in secure https web server. System configuration and viewing of realtime data can be performed from anywhere in the world.
Smart Devices

Internet capable devices with built-in LTE modem, LAN to connect and send the data to the cloud. The devices either interface the measurement systems or digital sensors to relay the measurement data to the cloud servers. Data streaming is done whenever the communication is possible and eliminating data loss due to possible communication outage.
Cloud Servers
Our cloud system is flexible for subscription with monthly payment for single/multiple devices up to fully deployed on-premise installation on customers’ own servers.
24×7 monitoring of the structure can be assigned to the intelligent software and any occasion that needs engineering attention will be automatically alerted by various means.
Intelligent back-end software and smart use of computational resources eliminate continuous, traditional manned monitoring, increasing productivity.
Analysis Software
We provide Operational Modal Analysis (OMA) software, ARTeMIS Modal. ARTeMIS Modal is the most powerful and versatile tool for Operational Modal Analysis available today. Its ability to produce validated modal parameter estimates, based on parallel analysis of up to seven different analysis techniques, makes it the natural choice in mission critical applications.
Operational Modal Analysis is also called output-only modal analysis, ambient response analysis, ambient modal analysis, in-operation modal analysis, and natural input modal analysis. No matter the name, the idea is the same: Conduct a modal analysis without knowing and/or controlling the input excitation. This modal technology is capable of estimating the same modal parameters as the traditional known techniques.
The modal parameters are mode shapes, natural frequencies and damping ratios. Some think that Operational Modal Analysis just is another name for Operating Deflection Shapes, ODS. This is not the case. Operational Modal Analysis separates noise and inputs from the outputs and returns the unbiased modal information only.
The Operational Modal Analysis are Multiple Input Multiple Output, MIMO, techniques. This means that the techniques are capable of estimating closely spaced modes and even repeated modes with a high degree of accuracy. Traditional modal analysis techniques are typically Single Input Multiple Output, SIMO, or Multiple Input Single Output, MISO, or in rare cases even Single Input Single Output, SISO. Such testing procedures will not be able to find repeated poles due to the lack of mode separation.
Vibration shakers and impact hammers are impossible as excitation sources when it comes to in-situ testing of offshore platform structures. In cases like this, the traditional modal analysis fails, because there are a number of unknown inputs acting on the structures. What is a problem for traditional modal analysis is a strength for Operational Modal Analysis. The more random input sources there are, the better the modal results gets. Since the real strength of the technology really lies in the in-situ testing, it is no wonder why the technology is called Operational Modal Analysis. Another important features that comes for free are that the estimated modes are based on true boundary conditions, and the actual ambient excitation sources.
Damage Detection
ARTeMIS Damage Detection module consists of two different damage detection algorithms that have been developed for long-term monitoring of structures. The algorithms are robust to the natural change of a structure’s dynamic behaviour due to the changes of ambient conditions and can be set up to not reacting on such changes. The plugin also includes a Control Chart that, as input, can take a user-definable set of damage indicators and unify them to a single control value with corresponding statistical based threshold. This control chart can automatically notify (alert) when the threshold is being passed after an analysis. The notification can be sounds, emails or web service calls to third party systems.
The features are summarised below:
- Classic and Robust Damage Detection.
- Automatic damage indicator updates when new measurements are uploaded.
- Reference State Validation for visual validation of the null space estimation of the reference state model.
- Hotelling Control Chart unifying damage indicators into a single indicator with a single statistical based threshold.
In the figure below, the damage detection is demonstrated using data from a bridge in Italy, that was measured for a period before damaging it. There are eight reference measurements that are presented by the first eight green vertical bars in the diagram.
The level of these bars shows the level of the damage indicators under normal conditions. From the first six measurements, a baseline (reference) model is determined by the module, and a threshold is automatically estimated based on the statistical evaluation of the damage indices of the six reference measurements.
As seen, the last two reference measurements stay under the threshold which indicates that the bridge is still undamaged. The remaining 14 measurements are all acquired after the bridge experienced damage, and the associated damage indicators all pass the threshold significantly and indicate a permanent damage.


Model Updating
Continuously updated model, automatically, with measurements and analysis results is crucial to establish a digital twin of the structure in question.
Model updating works by modifying the mass, stiffness, and damping parameters of the FE model until an improved agreement between FEA data and test data is achieved. Unlike direct methods, producing a mathematical model capable of reproducing a given state, the goal of FE model updating is to achieve an improved match between model and test data by making physically meaningful changes to model parameters which correct inaccurate modelling assumptions. Theoretically, an updated FE model can be used to model other loads, boundary conditions, or configurations (such as damaged configurations) without any additional experimental testing, also known as digital twin. Such models can be used to predict operational displacements and stresses due to simulated loads.
We provide FEMtools Model Updating software, which includes utilities and methods to update finite element models to better match reference test OMA. The updating methods are based on the use of sensitivity coefficients that iteratively update selected physical element properties (like for example material properties, and joint stiffness) so that correlation between simulated responses and target values improves. Response types can be static displacements, mass, modal data, FRFs, OMA parameters, operational data or correlation values like MAC. Parameters that can be updated are all mass, stiffness and damping properties used in the definition of the FE model. The resulting FE model can be used for further structural analysis with much more confidence. Additional physical parameters and inspection results can be augmented to create intelligent digital twin of the structure.
Ancillary Equipment
Besides the required instrumentation and software packages, for offshore structural dynamic monitoring may be complimented by the following additional equipment:
- Solar Power System: Some unmanned platforms have no access or restricted access to mains power supply. Solar power system with backup battery is necessary for continuous and autonomous data collection.
- Communication Gateways: For real time signal visualisation, it is helpful to have communication gateway to access the measurement system from the internet.
Please contact us to discuss your structural needs. Fine tuned measurement systems, analysis software and experience makes us invaluable partners in your quest for intelligent digital twins.